Wiring Electrical Systems – Eliminate Maintenance and Save Time
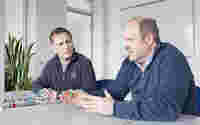
Drilling holes precisely and at high speed – this is the essential requirement the CNC drilling machines from Schmoll Maschinen GmbH have to meet.
The machines produced by this mid-sized company are used globally in electronics manufacturing. Numerous electronic devices, from smartphones to flat screen TVs, contain PCBs that were manufactured using this equipment. When wiring the electrical systems, Schmoll relies on TOPJOB® S Rail-Mount Terminal Blocks with push-in spring pressure connection technology from WAGO.
The Benefits of WAGO for You:
The right actuation variant of WAGO’s preassembled TOPJOB® S Rail-Mount Terminal Blocks is available for any application
Reliable, easy, intuitive handling with Push-in CAGE CLAMP®
The WAGO Smart Printer prints marking strips in seconds