Getting efficient shunting locomotives without negative impacts
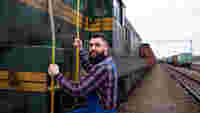
German freight traffic would practically come to a standstill without diesel-powered shunting locomotives. The Voith technology company has developed a sophisticated start/stop system to reduce the high idle times that often exceed 60 percent. The special difference here: ‟OnEfficiency.StopStart“ can be retrofitted and adapted to different product series of any manufacturer. This can save fleet operators an average of 11,000 liters of fuel annually and 30 tons of CO2 – for every vehicle that is. Non-interference with safety functions and, thus, protection of the locomotive is achieved technically using relay and optocoupler modules from WAGO.
When you imagine a train running you most likely also see an overhead line in the picture in your mind. This is because anywhere you see tracks, the scene is also marked by catenary line systems – or so you would think. But it's not always that way: Only around 60 percent of the German railway system is electrified, not even including freight traffic. In particular in marshalling yards without catenary systems, the combustion engine continues to rule.
Enhancing efficiency in freight traffic – with interface electronics and automation technology from WAGO:
Relay and optocoupler modules ensure freedom of interference with safety functions.
Compact, modular solutions for non-air-conditioned control cabinets
Standard-compliant technology stands up to mechanical loads and the most extreme ambient temperatures.