Digital und unabhängig mit MTConnect
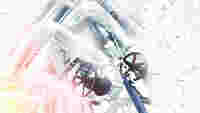
Der digitale Wandel fordert die zunehmende Vernetzung von verschiedenen Unternehmen, Produktionsstandorten, Maschinen und Komponenten. Nach und nach richten Hersteller ihre Maschinen deshalb auch auf den Austausch von Informationen aus.
Doch viele Maschinen, die aktuell in der Prozessindustrie im Einsatz sind, agieren noch als in sich geschlossene Einheiten. Größtenteils verfügen die Maschinen zwar über Sensoren zur Erfassung, etwa von Temperaturen, Sollwerten und Zykluszeiten. Dennoch fehlt ihnen die Fähigkeit, diese wertvollen Daten weiterleiten zu können. Damit könnte die Digitalisierung bereits in der Maschine enden.
So profitieren Sie von MTConnect:
- Die digitale MTConnect-Schnittstelle für den WAGO-Controller PFC100 ermöglicht die Vernetzung von Maschinen über einen lizenzfreien Open-Source-Standard.
- MTConnect als universelle digitale Schnittstelle basiert auf einem einfachen ETHERNET-Standard und lässt sich so problemlos in vorhandene Maschinen integrieren.
- Das einfache Konzept erlaubt Unternehmen mit komplexen Maschinen und Prozessen die mühelose Digitalisierung ihrer Fertigungsumgebung.