Automated DIN Rail Mounting with Robots
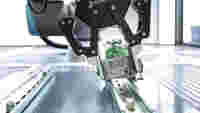
Robots with intelligent programming instead of a costly system for automated DIN-rail mounting: The “pitasc” software tool from Fraunhofer IPA makes this possible, allowing robot programming with force regulation by means of individual program modules. A joint research project between the institute and WAGO shows how an application for DIN-rail assembly is possible.
A lightweight robot picks up a plastic part with its two-finger gripper, guides it to the component to which it is to be attached and can snap it firmly into place using a tilting motion with force regulation. If the mounting application ever needs to be reconfigured, there is no need to reprogram the movements. Programming is workpiece-specific, and the force regulation allows intelligent compensation for component and position tolerances. The application just described has been implemented by researchers at the Fraunhofer Institute for Manufacturing Engineering and Automation (IPA). The institute has been working on solutions for fully or partially automated assembly for many years. After all, this production step is notoriously still largely carried out by hand: In 2020, only about one in ten of all robots sold worldwide worked in assembly. Challenges such as small batch sizes, a high number of variants and numerous individual processes often make it difficult to implement cost-effective assembly automation.
The Benefits for You:
Innovative: Automated DIN-rail mounting with robots in practice
Unrivaled: TOPJOB® S Rail-Mount Terminal Blocks used for automated control cabinet component placement
Easy: Completely eliminates manual work steps, saving time
Versatile: Thanks to the wide range of rail-mount terminal block variants, robots can perform assembly in a structured way