Playing It Safe with the Power Supply
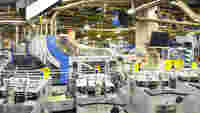
Protection with Fieldbus Couplers from WAGO
- Power Supply for Machines
- Remote Monitoring of the Circuit Breakers
- Alerts – Detailed and around the Clock
- Easy Retrofitting and Potential Expansion
There are multiple supply lines from the medium-voltage network on the Schweinfurt facility grounds. They supply the transformer substation, which has just under 100 transformers, and these in turn supply around 30 low-voltage main distribution boards, which provide the power to the facility’s manufacturing machines. “Power supply safety and reliability is particularly important to us,” explains Julian Kübler, who is responsible for monitoring the medium- and low-voltage transformers at the Schaeffler factory in Schweinfurt. Circuit breakers separately isolate the outputs for the electrical loads in the systems. Each circuit breaker is accommodated in a control cabinet in its own array. For loads with lower power, several small circuit breakers are sometimes mounted in an array. A typical system consists of two to three regions with 15–20 arrays with a total output of up to 2,000 kVA.
During the setup of the low-voltage systems in 2015, a malfunction alarm was also included. Kübler describes the disadvantages of the old system thus: “Previously, the systems could only trigger a collective failure, which was then transmitted to the plant’s security office.” In the process, a ring circuit transmitted the alarm to all circuit breakers, so it was impossible to determine remotely which outflow was actually affected. In the first step, to ascertain precisely which circuit breaker triggered the fault, the message outputs from all circuit breakers were sent to an additional control cabinet close to the system. A controller processed the signals and forwarded corresponding messages to the control center. “The wiring expense for this solution was, however, extremely high,” explains Kübler, “so we looked into alternatives.”
The Schaeffler employees from the plant facilities department hit the jackpot with WAGO. Hardware such as the fieldbus couplers and I/O modules from the modular WAGO 750 I/O-SYSTEM allows a significantly more elegant solution for fault message processing. In addition, each control cabinet array in the system was retrofitted with a PROFINET coupler. This includes a digital input module with 16 channels, which thus has sufficient capacity to evaluate all messages from the circuit breaker in detail. A central controller functions as the master in PROFINET and reads the signals from the PROFINET coupler; additional processing and the control center linkage function just as before. The use of WAGO’s PROFINET coupler has one essential advantage for Kübler: “All we have to do is connect the couplers with patch cables from array to array. Since we use a ring topology, the system functions even if one patch cable is interrupted.” The cables are connected directly through internal channels in the control cabinet. Expensive wiring through the raised floor of the system is no longer necessary. Since both the control lines and power cables are routed from the circuit breakers to loads through the common cable connecting compartment, the respective outflows would have to be disconnected from the power in order for signal cables to be laid.
Julian Kübler is responsible for supervising the facility systems at Schaeffler’s Schweinfurt location.
The employees can monitor the status of all circuit breakers at all times from the control center, which is installed in the maintenance workshop. The status of the entire power supply is transparently visualized here. The new fault message system, which has been installed in three of the low-voltage systems so far, provides significantly more functions than the previous solution. In case of a fault, the maintenance employees know which circuit breaker has been triggered and which malfunction is located where. The security center likewise receives more detailed error messages and can thus provide the on-call service workers with important information before they arrive at the facility. “In this way, we can increase the safety of our low-voltage power supply, and thus the uptime of our production systems,” says Kübler happily.
The fieldbus coupler and suitable input modules can be easily integrated into the control cabinet.
by Frank Sünkel | 2016-10-12
Photos: Anand Anders/vor-ort-foto.de
WAGO at Work
Customer Applications from the Area of Production Technology
As a partner and innovation leader, WAGO implements many interesting projects. Learn more about our creative and efficient production technology solutions.
CNC drilling machines from Schmoll are used worldwide. TOPJOB® S Rail-Mount Terminal Blocks from WAGO are used for wiring their electrical systems.
Specialized machine construction demands modular solutions for connecting actuators and sensors. WAGO’s product range is attuned to these demands.
At Nordson, a wide variety of machines are produced in record time. WAGO’s automation technology and e!COCKPIT Engineering Software make this possible.
Recommended Reading
More Solutions
WAGO’s automation and electrical interconnection technologies are not only represented in production technology. Learn what solutions WAGO offers in other industries.
Power Engineering
The energy sector is facing great challenges in every area. Intelligent networking and innovative solutions from WAGO help meet these challenges.
Marine and Offshore
Whether for applications in shipbuilding or in the on/offshore sector, WAGO combines innovation with reliability and flexibility, making it the preferred partner of many ship suppliers.