Maintenance in Record Time
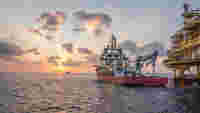
System wiring on drilling platforms is a major challenge. The WAGO-X-COM®S-SYSTEM reduces work on site to a minimum.
If an important technical component fails on an offshore drilling rig, the emergency is often dire. In most cases, a specialist has to be flown in as fast as possible via helicopter, and then often has to perform complicated repairs under extreme conditions. A prominent European drilling equipment manufacturer sought a maintenance-friendly and economical alternative, and developed a solution using components from the WAGO X-COM®S-SYSTEM.
Deck Handling and Cranes – This Is How WAGO Lends a Hand:
- With the WAGO-X-COM®S-SYSTEM, system wiring on site is reduced to a minimum.
- Exchanging individual modules of the rail-mount terminal block system is easy, fast and safe.
- One to three rows of printable marking strips ensure unmistakable identification of individual sub-assemblies.