The Key to Greater Sustainability and Efficiency Lies in Networking
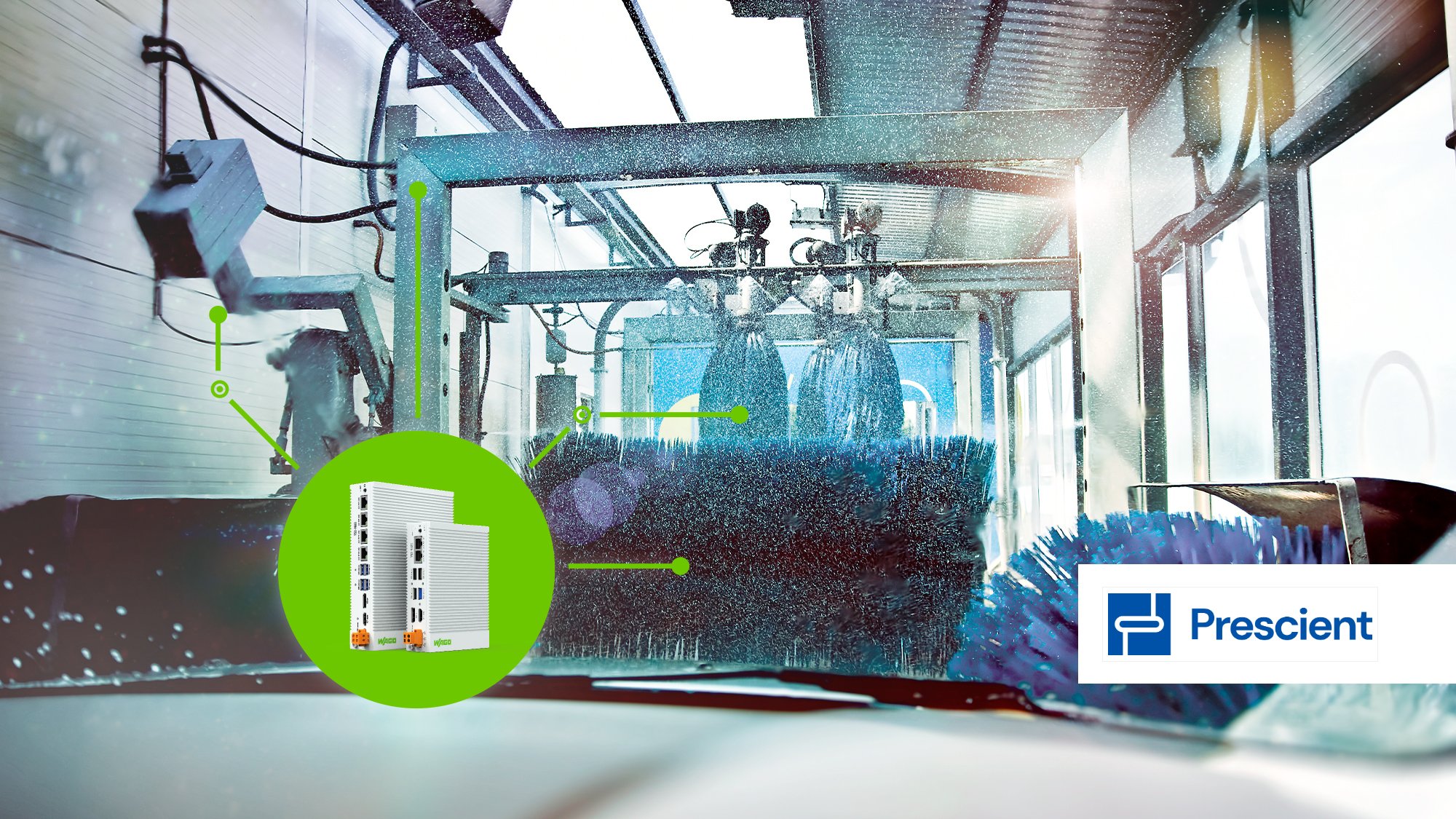
The Internet of Things is a big term: In industry, the concept promises flexible implementation of machine communication to make your own production future-proof. However, this is still not the standard because the path from the field level to the industrial cloud requires corresponding infrastructure. Currently, the greatest challenge for using the IIoT is providing the data: The relevant parameters must first be defined, digitally recorded and processed before they can be stored in the cloud or on the server. So the right infrastructure is essential to make the IIoT possible.
In order to achieve the necessary holistic networking from the field level up to the cloud, different actors must work together efficiently. Therefore, WAGO has established an international IoT partner network, a strategic technological initiative with collaborators from the low code/no code, security, OT/IT integration and IT software sectors. In addition, technology partners are also within the network to enable the mass deployment of WAGO hardware, for example. WAGO thus bundles the expertise of many different companies and extends its open Linux-based controllers with the domain knowledge of the respective partners, allowing customers to receive an integrated end-to-end solution. In the Internet of Things, no two solutions are the same: Depending on the application, systems tailored to requirements are necessary to obtain the optimal result. This is as true in industrial production as in everyday installations, such as a car wash.
Chemicals Optimization via Data Acquisition
Customers face challenges in many areas that can be solved with the Industrial IoT. One chemical manufacturer had the specific problem of implementing intelligent data solutions in a mass deployment for its customers, in this case, car wash operators. The manufacturer’s goal was to monitor the consumption of chemicals, reduce service calls and inventory levels, and optimize the supply chain. However, data acquisition and processing in a car wash is a complex undertaking, similar to that in industry. Because, on the one hand, it takes both highly specialized domain knowledge from car wash production and process technology, and, on the other, automation and programming knowledge.
Optimal data use requires more and more computing power, with corresponding demands on databases and analysis/optimization algorithms.
In a car wash, linked machines or system parts interact with each other: The cleaning systems must be adjusted to the lane and rotate without causing damage. In addition, cleaning agents must be used sparingly. After all, chemicals in car washes are not only expensive, they can also pollute the environment. Up to now, the recording of chemical consumption in car washes has been sporadic. Therefore, the chemical manufacturer and car wash operator wanted to obtain a precise breakdown of consumption. Implementing corresponding systems requires specialized companies, as the following example shows.
With this comprehensive challenge, the chemical manufacturer approached WAGO, as expertise from the automation and manufacturing industries was needed. A change was made from the previously used hardware to a WAGO PFC200 controller, in combination with a WAGO Edge Computer as a path to the cloud. WAGO relied on expertise from the IoT partner network to provide an application-specific mass deployment. Specifically, Prescient was included – a company headquartered in Concord, Massachusetts. Prescient empowers data engineers to design, prepare and deploy low-code edge data solutions from the cloud for operation at the edge.
The application was implemented using the in-house Prescient Designer software, which is based on NodeRED, allowing fast and easy implementation of complex edge projects. This allowed a fast and efficient smart data solution to be implemented, which starts at the field level. There, operating, machine and logbook data can be recorded via digital or analog signals, various fieldbuses or energy meters, among other things. The edge devices and the controller process the data into a model before it is analyzed in the industrial cloud. A Web-based application is used as a front-end solution, which is fed by the data obtained from the back-end. This modern software architecture approach, the separation between front and back ends, will allow both the automation and the Web application to be processed independently and remain updated in the future.
To optimally integrate Prescient Designer, the hardware must work natively with NodeRED. Therefore, the WAGO PFC200 was the best possible choice with the open-source capabilities of its Linux operating system. The PFC200 uses a Docker container that provides access to the I/O modules via Modbus. Containerization, e.g., with Docker, offers customized configuration options for programming through access to ready-made containers and integration of third-party elements. Docker containers, optimized for the WAGO hardware, are freely available on the WAGO GitHub account; this is a good example of how open source offers customers more flexibility in finding solutions in general.
The Digital Twin in the Car Wash
Using the approach described above, it is possible to generate a digital twin from the physical process of supplying chemicals for car wash systems. The digital twin displays the recorded data in real-time, allowing adjustments to be made that increase the efficiency and sustainability of one’s own work process. Thus, trends that provide further information about resource consumption can also be identified in combination with the data that has already been collected. WAGO and Prescient have found a way with the chemical manufacturer to generate a digital solutions business for a traditional hardware supplier (in this case, chemicals).
Thanks to the Internet of Things, the consumption of chemicals can now be optimized and used more sustainably. In addition, forecasting depleted chemicals and service calls is also possible. On-site employees can plan repairs and deliveries, eliminating the need for shutdowns. The car wash thus becomes an example of a large system that already provides a lot of data from the ground thanks to the networked machines.
What applies to car washes can also be transferred to the industrial production process. This is also the case, when a large amount of data accumulates during production, from which valuable conclusions can be drawn about the production efficiency. More and more computing power is needed to accomplish these tasks. Modern edge devices process the data in real-time, providing the corresponding performance for analysis and optimization algorithms. The main advantage of edge devices is that they ensure latency-free data processing, and the data can be aggregated and pre-processed accordingly to optimize data transfer to possible cloud infrastructure and reduce costs. This reduces the load on the controllers, allowing them to focus on their original control tasks with low latency and high determinism.
Open Automation Leads to the Goal
Beyond this solution-driven approach, the future of industrial production lies in linking of OT and IT. Depending on the application area, the Industrial IoT can also be used in building or energy technology – anywhere that the value-added chain can be networked and optimized.
Openness at all levels of automation plays a special role in this. Therefore, WAGO relies on CODESYS V3 for programming, which opens up many possibilities. This allows a continuous connection from the field level to the cloud to be implemented, which is based on a comprehensively networked infrastructure. More than 500 I/O modules and interfaces enable adaptation to different requirements. Of course, IT security is also important: All development processes in automation at WAGO meet the IEC 62443-4-1 requirements. At the same time, standards such as OpenVPN, SSL, SSH, IPsec and firewall increase security when using WAGO controllers.
In times when 100% machine availability is the standard, security – in addition to intelligent data use – is indispensable. At the same time, demand forecasts and supply chain transparency implemented through data collection are also becoming increasingly important in times of economic instability. The Internet of Things will lay the foundation for the successful industry of tomorrow – and do so transparently, networked and reliably.
Industrial IoT
Optimal Data Utilization in the Field Smart processes require more and more computing power, with corresponding demands on databases directly in the field. WAGO offers the right hardware for any edge application.
Availability for machines and systems: Thanks to top performance, low power consumption, multiple interfaces, compact dimensions and a high degree of safety, our programmable logic controllers (PLCs) offer cost-effective automation solutions for numerous applications.