Dynamic? Absolutely!
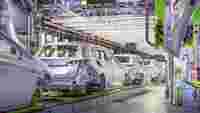
The Benefits for You:
- Dynamic, automated adaptation of the tripping current to the current load situation
- Reliable tripping in the event of faults
- Power supply overdimensioning can be avoided
Rethinking 24 Volt Circuit Protection
12 January 2022As the level of automation in production and process systems increases, the number of loads powered by 24 volt direct current – controllers, sensors and electric motors – also continues to increase. The current in these circuits is usually provided by power supply units. Power supply units cut the power when a nominal value is exceeded and connected loads fail; therefore, circuit breakers protect individual components or groups of components in order to limit the effects of overcurrents and short circuits. However, conventional automatic thermal-magnetic circuit breakers require a high overcurrent to reliably trip. The necessary cut-off current may even be greater than the maximum current provided by the power supply. That makes fast, reliable shut-down in the event of short circuit impossible. In addition, capacitive loads, long cables or the simultaneous start-up of several 24 volt loads may cause additional challenges for the power supply and fusing.
An Electronic Circuit Breaker That Can Do Everything?
Electronic circuit breakers (ECBs), which use semiconductors as switching components and continuously measure the current, respond to changes in current values with much greater sensitivity. These circuit breakers react as soon as the output current exceeds the nominal current value, which is configurable. The tripping time depends on the magnitude of the overcurrent. A microprocessor handles the processing and calculation of the tripping time and is responsible for tripping the semiconductor switch. This can switch off precisely and quickly when secondary-side overcurrents occur. Electronic circuit breakers are also able to switch the power off at or above a specified value – for example, 1.3 or 1.5 times the nominal current – within a specified period of time. When capacitive loads are applied, current spikes are handled without interruption. More sensitive response behavior like this, along with the active current limitation, also allows electronic circuit breakers to be used with greater maximum cable lengths.
Last but not least, this type of circuit protection offers a substantial benefit for the dimensioning of the power supply. In contrast to conventional circuit breakers, a smaller buffer in the output load dimensioning suffices for the maximum overload range of the power supply. For example, the constant current mode or Power Boost behavior represents one element of the overload behavior. Because traditional circuit breakers require high overcurrents for them to trip in the event of a short circuit, their power supplies require corresponding overdimensioning. With the Pro 2 Power Supply, that’s not necessary. “The overall power requirements may, under certain circumstances, be several times the current required for normal operation,” explains Frank Sellke, Business Development Manager for Interconnection and Interface Products at WAGO. “This overdimensioning incurs costs, and beyond that, it requires more space in the control cabinet.”
Intelligent Load Management Becomes Dynamic
The WAGO Pro 2 Power supply combines the features and benefits of ECBs with communication capability and simple, versatile device parameterization. With the attachable communication module, the Pro 2 Power Supply can provide information about current data, such as base loads or peak loads, at any time via standardized protocols. In addition, the configuration of the power supply can be modified within milliseconds, even during ongoing operation. Parameters like overload behavior, output voltage and the tripping value for the ECB function can adjusted.
In connection with a controller, this opens up completely new possibilities: dynamic protection of load circuits! The way it works is both simple and ingenious: If multiple loads are attached to one load circuit, the different capacitive and inductive loads cause significant current fluctuations during start-up and shut-off operations. Even with ECBs, the only way to handle this is with overdimensioning and staggered switching times. “That’s not the case with the Pro 2 Thanks to its communication features, the characteristic value for the circuit protection can be automatically adjusted to the present current load,” explains Florian Kothe, Business Development Manager for Interface Products at WAGO. “The PLC, which controls the on and off switching of the loads, informs the power supply of the load value to be expected in the next 20 milliseconds. The value is adjusted accordingly with a configurable buffer of 3 to 5 %.“ The result is circuit protection that functions safely and reliably at every operating point – without overdimensioning!
Florian Kothe, Business Development Manager for Interface Products at WAGO
Predicting Damaging Events
Beyond higher efficiency, there are additional benefits you might not initially expect from a power supply unit. With its fine-grained sensitivity, this dynamic circuit protection setup can also support predictive maintenance strategies. Since it always dynamically maintains the nominal value just above the expected current, it can be used to detect noticeable load current deviations. For example, if a connected motor is drawing 4.5 amps of current instead of the expected 4, this may indicate a mechanical problem, such as the early stages of a shaft jam caused by insufficient lubrication, imbalance etc. With its current measurement functionality, the Pro 2 can be used to detect such threats of damage.
The Pro 2 can even be set up with a configurable advance warning threshold to trigger a notification before the dynamic characteristic value of the circuit protection is exceeded. As a result, instead of waiting for a fuse to trip – possibly interrupting operation – operation or maintenance teams get a system notification of the threat of a fault in the near future. “Thus, this dynamic solution not only contributes to greater safety in equipment and system operations, but also allows more predictable maintenance, longer operating times and optimization of operating efficiency, in addition to smart performance management,” says Business Development Manager Sellke, summarizing the benefits for users.
About the authors:
Frank Sellke has worked at WAGO in Minden since 1994. He began as a technical consultant and currently works in Business Development for Interconnection and Interface Products. Over the course of his career, he has visited customers and colleagues in close to 50 countries. He especially appreciates the fact that WAGO is willing to explore new approaches and anyone can draw on their own personal strengths and preferences to contribute to these innovations as part of a fantastic team.
Florian Kothe is Business Development Manager for Interface Products at WAGO and functions as the human interface between Product Management, Marketing and Sales. Ever since he went on a factory tour at the headquarters in Minden as a college student, he knew that WAGO would be his top choice of employer. Since he joined in 2018, he has enjoyed the work environment and potential for individual development that WAGO offers.
Frank Sellke, Business Development for Interconnection and Interface Products
WAGO's Pro 2 Power Supplies – Control cabinets are transforming because the requirements (both quantitative and qualitative) placed on them are continually increasing. Greater networking, rising energy costs and increasing customization require economy, speed and flexibility in a minimal footprint for control cabinets.